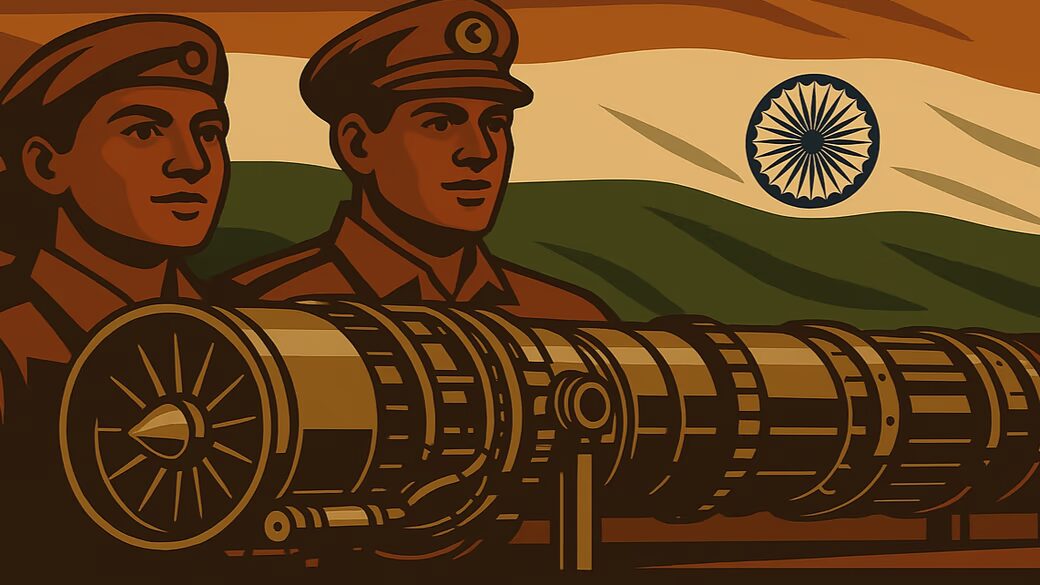
The Defence Research and Development Organisation (DRDO) announced on Tuesday that it is testing the indigenously built Kaveri jet engine in Russia, with approximately 25 hours of testing remaining. The slots have to be given by the authorities there. The interest in the Kaveri engine has been reignited by a social media trend urging the government to #FundKaveriEngine project.
This breakthrough opens the windows for India to dream big yet once again about independence from foreign engine technologies in an era of global military self-reliance. Kaveri engine is being forced to be modified to succeed in events like AMCA and stealth UAVs. This indeed speaks volumes about India’s increasing maturity in fundamental aerospace fields.
ALSO READ- Project Kusha
History of the Kaveri Engine-
- The contract was given to the aircraft engine project under Kaveri in 1986 to evolve the powerplant for the first indigenous fighter.
- Conceived by the GTRE, it was considered a strategic enabler to reduce import dependence on Western engines.
- The initial designs of the engine were based on European and Russian turbofan technology but were customised for Indian conditions.
Key Challenges in Early Years:
- The lack of experience in super-temperature metallurgy and jet propulsion dynamics afflicted the program.
- Post-1998 nuclear test sanctions limited access to the advanced materials and software needed for validation.
- The test infrastructure, such as wind tunnels and altitude simulation rigs, had to be set up, creating considerable delays.
- Such limited success notwithstanding, the program did amass a wealth of know-how in areas relating to combustion science, blade cooling and fluid dynamics.
Design and Technical Specifications-
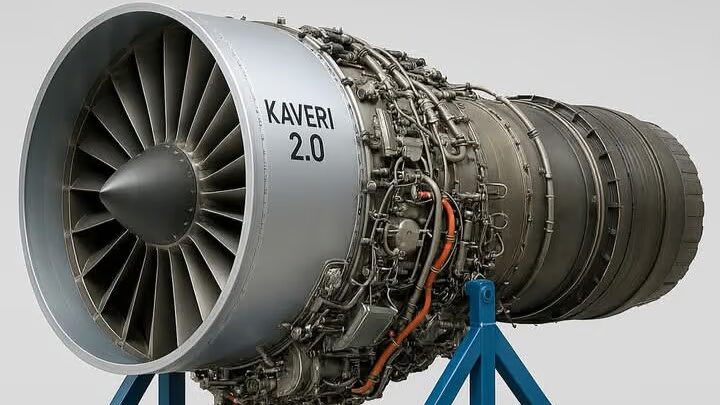
Kaveri engine is a less border strip afterburning turbojet engine optimised for use on high-class warplanes.
Core Specifications:
- Twin-spool: axial-flow turbofan with afterburner.
- Thrust (Dry): 52 kN; With Secondary Combustion Chamber: ~81 kN
- Weight: Approx. 1100 kg
- Cold Thrust: 0.16:1, making it suitable for supersonic warplane regimes.
- Length: 3.5 meters; Diameter: ~90 cm
Key Design Features:
- Advanced jet engine design plays an eminent role in the monocrystal turbine fans.
- Full Authority Digital Engine Control (FADEC) is employed for real-time thrust modulation and engine diagnostics.
- This is attributed to the ring combustion chamber that ensures an improved coupling of fuel and air as well as combustion.
- Servicing downs and the modular architecture provide for easy replacement of critical subsystems like the turbine and compressor.
Manufacturing and Development Partners-
Lead Agency:
This R&D is led by the Gas Turbine Research Establishment (GTRE), which was built at its inception and is aided by the big infrastructure of DRDO.
Industry and International Cooperation:
Casting, forging, and precision fabrication of critical components are being contributed by BHEL, Godrej Aerospace and Midhani.
International partners like Safran (France) have now stepped in to assist with material science and noise reduction technologies.
Collaborations are being explored with academic institutions for AI-driven engine health monitoring systems.
This wide stakeholder network acts as the backbone of the aero-engine manufacturing ecosystem in India, which would have been virtually nonexistent three decades back.
Applications and Future Integration-
Original Purpose:
It meant that for the Tejas Light Combat Aircraft (LCA), the engine was decoupled from the program after failing to meet production benchmarks.
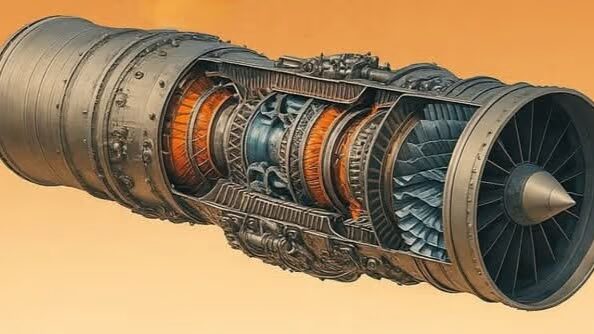
Present Status:
The dry variant (non-afterburning version) is thought to be most suitable for the Ghatak UCAV for its low heat signature and high endurance.
Future versions may power twin-engine configurations for AMCA Mk2, which is designed to be a 5.5-generation stealth fighter.
Defence planners are also assessing Kaveri variants for use in subsonic transport aircraft to reduce logistical dependency on imports.
In addition, consideration is being given to the export of drones or trainer aircraft powered by Kaveri derivatives under the Make in India scheme.
Development Timeline-
- 1986: The project is initiated with a budget of ₹382 crore.
- 1996-2004: Ground test validation and limited altitude trials.
- 2007: Engine fails critical trials; Tejas adopts the GE F404 engine.
- 2010: Flight testing carried out in Russia on the IL-76 platform under a joint program.
- 2014: Work starts on a dry version meant for unmanned platforms.
- 2021: India signs agreement with Safran for resurrecting & upgrading Kaveri.
- 2024-25: Confirmed high altitude performance; major milestone achieved.
Program notwithstanding some delays, has created a skilled workforce and infrastructure around high-performance propulsion.
Comparison with Other Jet Engines-
GE F404 (Tejas Mk1):
- Proven technology with many hours of battle proficiency.
- Backed by mature maintenance and a global support network.
- Still lacks the level of customisation that an indigenous engine offers.
GE F414 (Tejas Mk2, AMCA):
- Provides superior thrust (98 kN), allowing more payloads and supercruise.
- India’s decision to use it for AMCA reflects urgency, not a capability deficit.
- High costs and recurring dependence are strategic drawbacks.
Russian AL-31FP (Su-30MKI):
- High thrust and reliable, but maintenance-heavy.
- Indigenous production has reduced cost, but not strategic dependency.
- Integration with Tejas or AMCA is impractical due to size and weight.
Strategic Importance-
- A domestic jet engine capability reduces strategic vulnerability during war or sanctions.
- India spends billions on foreign turbojet engine imports; Kaveri could immediately cut prices.
- Enhancing domestic R&D through Kaveri creates spillovers in commercial aviation and space technology.
With potential military applications spanning from UAVs to manned jets, Kaveri is not just an engine, but a symbol of India’s aerospace ambitions.
Spin-Off Technologies-
- Blade Cooling Tech: Advanced air-cooling techniques for turbine blades have applications in thermal power plants.
- FADEC Systems: Software expertise gained can be used for electric propulsion control and AI-driven systems.
- Alloys and Ceramics: High-temperature materials developed for Kaveri benefit India’s space launch vehicles like GSLV Mk3.
- Acoustic Reduction: Research in low-noise engines opens doors to future civil aviation platforms.
These innovations collectively enhance India’s ecosystem of advanced manufacturing and R&D.
Criticisms and Roadblocks-
- Budget overruns and delivery delays have often drawn flak from policymakers and defence analysts.
- The lack of periodic public audits or performance whitepapers has raised transparency concerns.
- Overdependence on foreign test facilities, until recently, reflected infrastructure gaps.
Yet, these criticisms underscore the importance of a policy environment that supports innovation with accountability.
What’s Next?
- DRDO plans to merge Kaveri’s dry core with a new afterburner section optimised for stealth aircraft.
- Joint ventures with reputed company of this field may extend to AI-based engine diagnostics, enhancing flight safety.
- There is also talk of reviving the GTX-35VS variant for twin-engine drone systems or small transporters.
The integration of Kaveri into India’s future aerial platforms could significantly change the defence procurement landscape.
Conclusion-
The Kaveri engine project, once dismissed as a failure, is now being reborn as a testament to India’s persistence and innovation. Its technological breakthroughs, though delayed, have laid a solid foundation for future aerospace projects. The path to indigenous jet propulsion is complex and costly, but with Kaveri’s revival, India has proven that long-term vision and scientific perseverance can eventually close even the widest technology gaps.
With the right momentum, the Kaveri engine can evolve from a national aspiration to a global benchmark in indigenous propulsion systems.